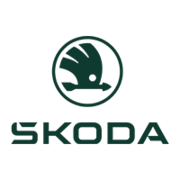
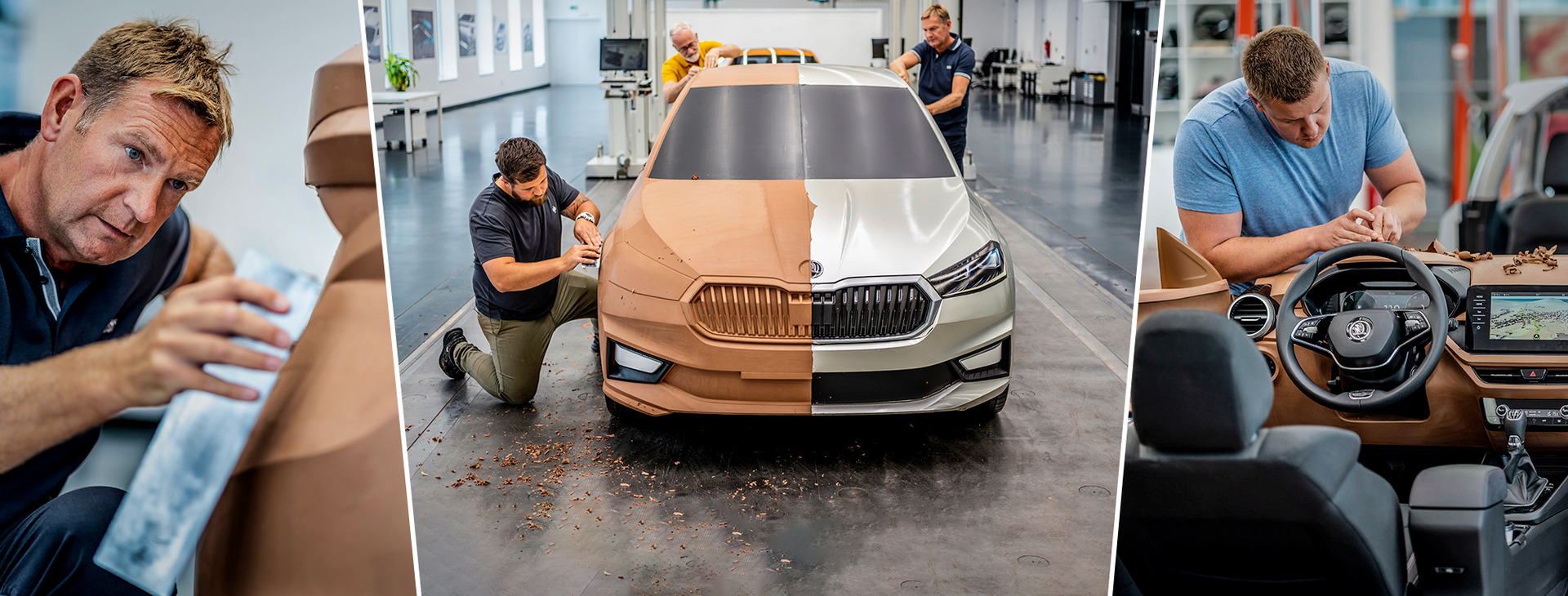
Tonkünstler: Die Bildhauer im Automobilbau
Im Wesentlichen geht es um eine Kombination aus technischen Disziplinen und Kunst. „Viele Mitglieder unseres Teams haben Kunst studiert oder verfügen über andere Erfahrungen im künstlerischen Bereich“, bestätigt Martin Bogner, Leiter der Abteilung EDM, in der Teams von Modellierern digitale und physische Modelle erstellen. Das Design Center in Česana (CZ) ist einer der am besten abgeschirmten Standorte von ŠKODA. Hier entstehen die Modelle zukünftiger Fahrzeuge oder Konzepte für Ausstellungen. Bei Serienmodellen werden die Fahrzeuge hier bereits Jahre vor ihrem ersten Erscheinen in der Öffentlichkeit hergestellt. Wenn die Arbeit der Modellbauer an einem bestimmten Auto abgeschlossen ist, bleibt das Ergebnis noch etwa zwei Jahre lang ein gut gehütetes Geheimnis. Liebhaber des Automobildesigns kennen die traditionellen Tonmodelle, mit denen Automobilhersteller das äußere Erscheinungsbild eines Fahrzeugs Schritt für Schritt entwickeln. Heutzutage werden diese Tonmodelle jedoch mit einer Reihe von eingefügten Teilen aufgewertet. Diese maßgeschneiderten Komponenten bringen die Modelle dem echten Auto optisch näher.
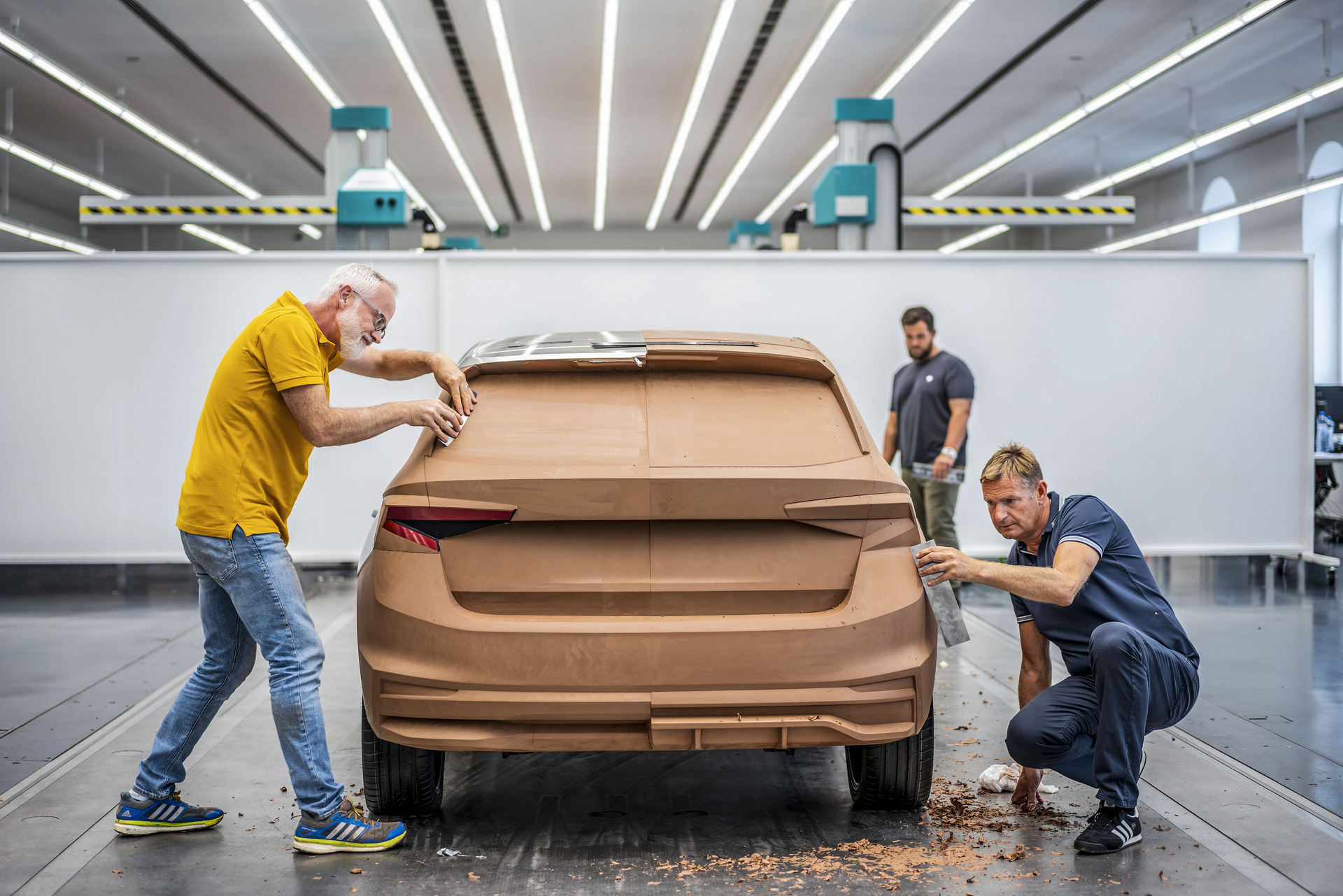
Wie es Martin Bogner ausdrückt: „Physische Modelle sind für uns nach wie vor sehr wichtig. Der Einsatz der menschlichen Hand ist in diesem Fall unverzichtbar. Wir verwenden die Modelle zur Feinabstimmung von Details, die wir in der digitalen Umgebung übersehen könnten. Auch bei der Freigabe des endgültigen Designs eines Fahrzeugs durch das Topmanagement kommen bei ŠKODA wie im gesamten Volkswagen Konzern nach wie vor physische Modelle zum Einsatz. Diese Präsentationen liegen ebenfalls in der Zuständigkeit unseres Teams.“ Der physische Modellbau bei ŠKODA AUTO wird von Vlastimil Pažout geleitet, der sämtliche Aktivitäten der drei Studios für Exterieur, Interieur und Komponenten verantwortet. Das für das Exterieur zuständige Studio ist der größte Arbeitsbereich im Modellbau – in der Halle finden bis zu sieben Modelle im Maßstab 1:1 Platz. „Wenn wir an Konzepten für Automobilausstellungen und künftige Serienfahrzeuge arbeiten, machen wir alles im Maßstab 1:1, weil manche Details in einem kleineren Maßstab möglicherweise nicht richtig zur Geltung kommen“, erklärt Vlastimil Pažout.
Die Besucher des Studios werden sich vielleicht über die großen Fräsmaschinen wundern. Mit ihrer Hilfe gelangt das Fahrzeug aus der digitalen in die physische Welt. Früher formten die Modellbauer die Fahrzeuge komplett in Handarbeit aus Ton. Heute übernimmt die Fräsmaschine die grundlegenden Arbeiten. Die Basis des Modells bildet ein mit Hartschaum bestücktes Stahlskelett, auf das eine Schicht aus Ton aufgetragen wird. Dazu wird der Ton in einem speziellen Ofen auf 50 bis 60 °C erhitzt. So kann er leicht verformt werden und entwickelt eine gute Haftung. Nach dem Abkühlen auf Raumtemperatur härtet er aus. Es gibt gute Gründe dafür, dass die Modelle nicht vollständig aus Ton hergestellt werden. Abgesehen vom extrem hohen Gewicht (die Modelle wiegen auch jetzt noch mehrere Tonnen) und den beträchtlichen Kosten könnte der Ton reißen oder sich sogar in ganzen Stücken ablösen.
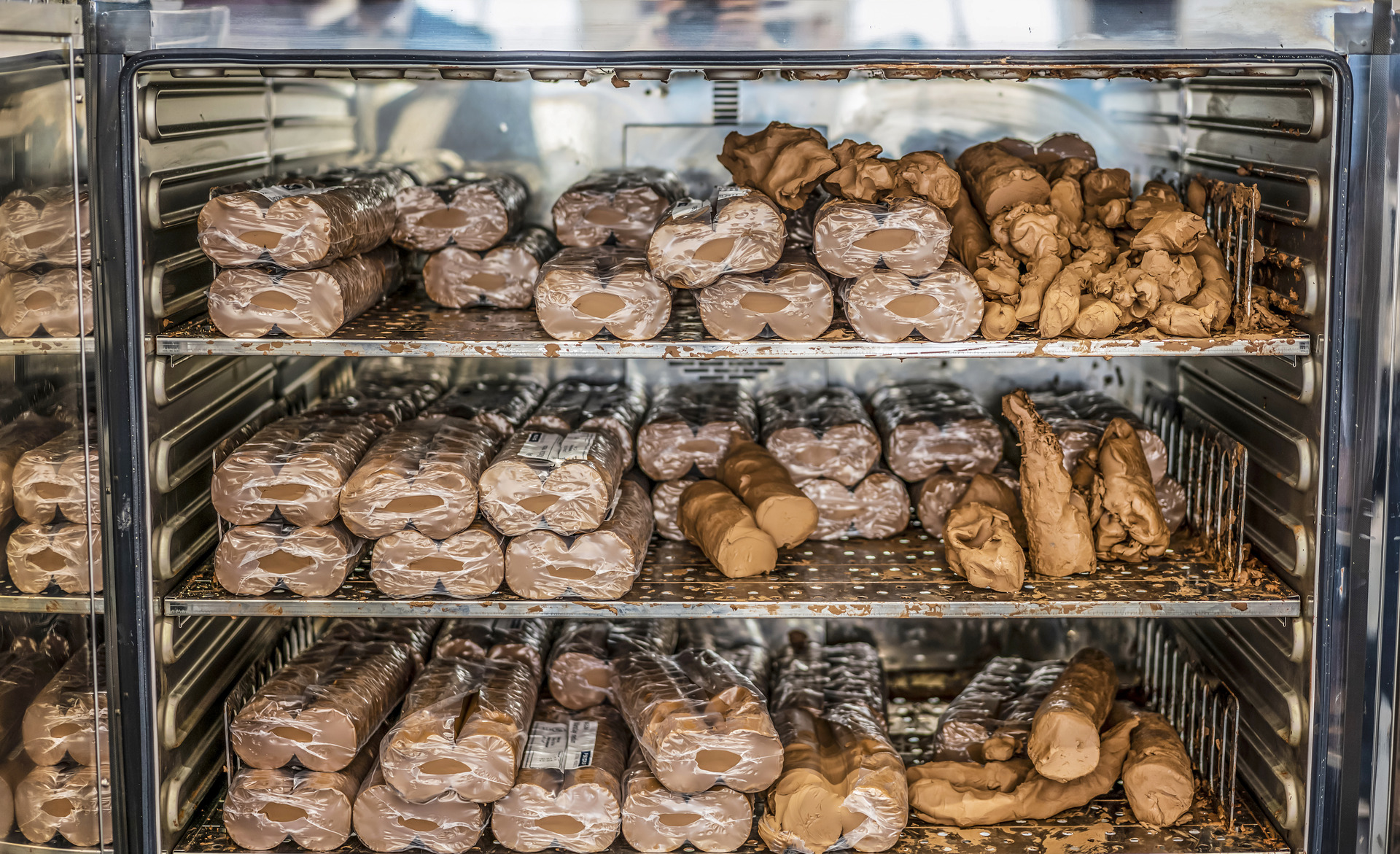
„Nachdem die Basisschicht aufgetragen wurde, schneidet die Maschine den Ton in die Grundform, die von den digitalen Modellierern in Zusammenarbeit mit den Designern entwickelt wurde“, sagt Vlastimil Pažout. Sobald das Objekt seine Grundform erhalten hat, beginnt die Arbeit der Modellierer. Mit Schabern, Messern, Spateln und anderen Werkzeugen feilen sie an den Konturen, die nach dem ersten Fräsgang in der Regel etwas scharfkantig und aufgeraut sind. Das Ergebnis ihrer Arbeit wird dann gescannt und in ein 3D-Modell umgewandelt, das in der Folge als Grundlage für weitere Fräsarbeiten oder Designvisualisierungen und digitale Präsentationen dient. Für jedes Fahrzeug werden mehrere Designalternativen entworfen, aus denen ein Favorit gewählt wird.
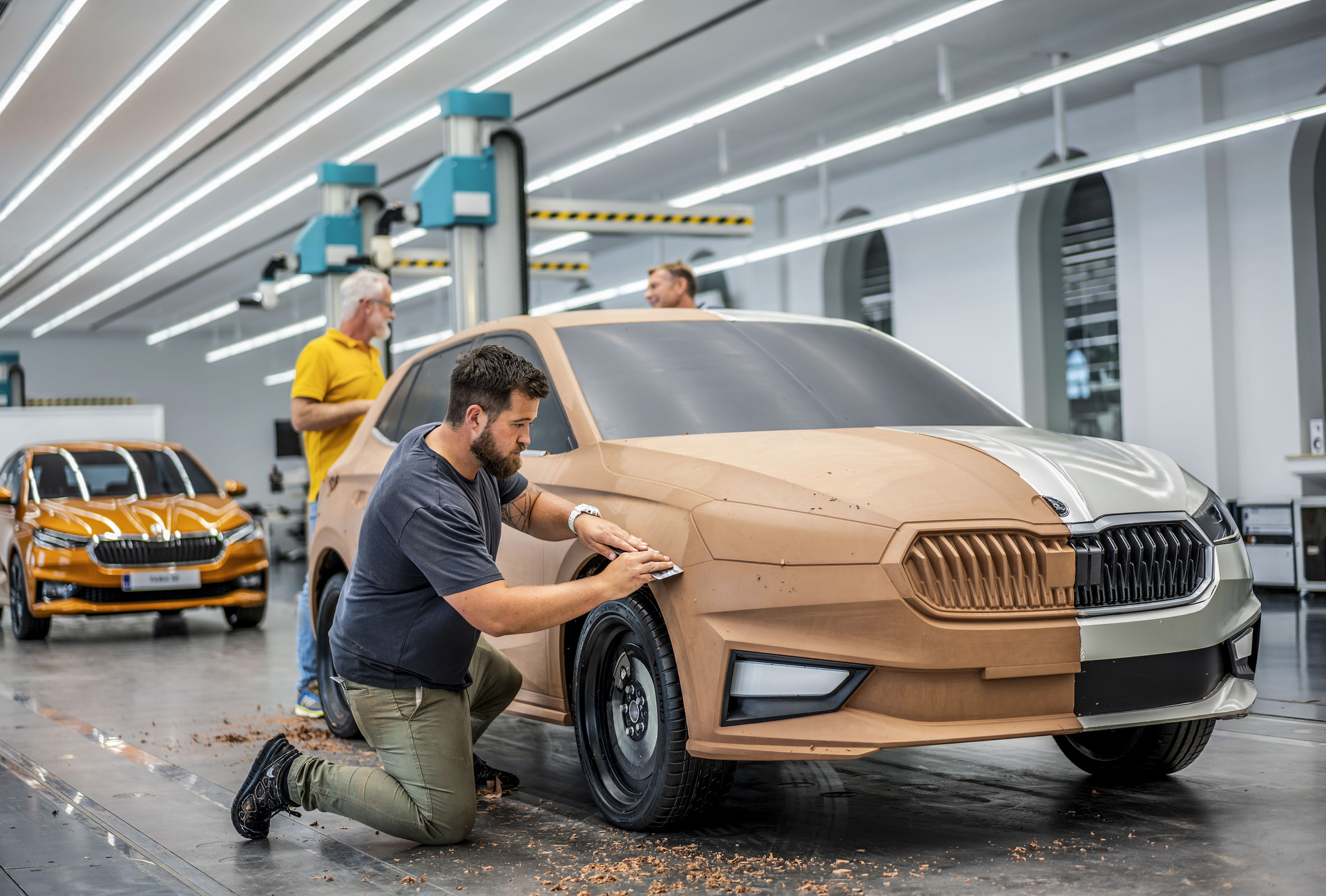
„Modellbauer sind Künstler und Meister ihres Fachs. In Zusammenarbeit mit dem Designer zeichnen sie ihre Skizzen in Ton. Dabei schöpfen sie aus ihren künstlerischen Qualitäten und ihrer Erfahrung. Gleichzeitig müssen sie sich perfekt mit dem Designer abstimmen“.
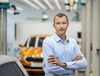
„Für das Interieur muss man sich mit der Textur vieler Oberflächen auseinandersetzen. Beispielsweise würden sich die Lamellen der Luftausströmer und andere Details kaum vom Rest des Interieurs abheben, wenn sie nur aus Ton modelliert wären“, erklärt Vlastimil Pažout. Einige Teile, wie etwa die Lenkstockhebel oder das Lenkrad selbst, könnte man überhaupt nicht aus Ton herstellen. Diese Teile werden beispielsweise auf 3D-Druckern hergestellt, penibel bearbeitet und dann von Hand zusammengefügt – das ist häufig eine knifflige Arbeit.
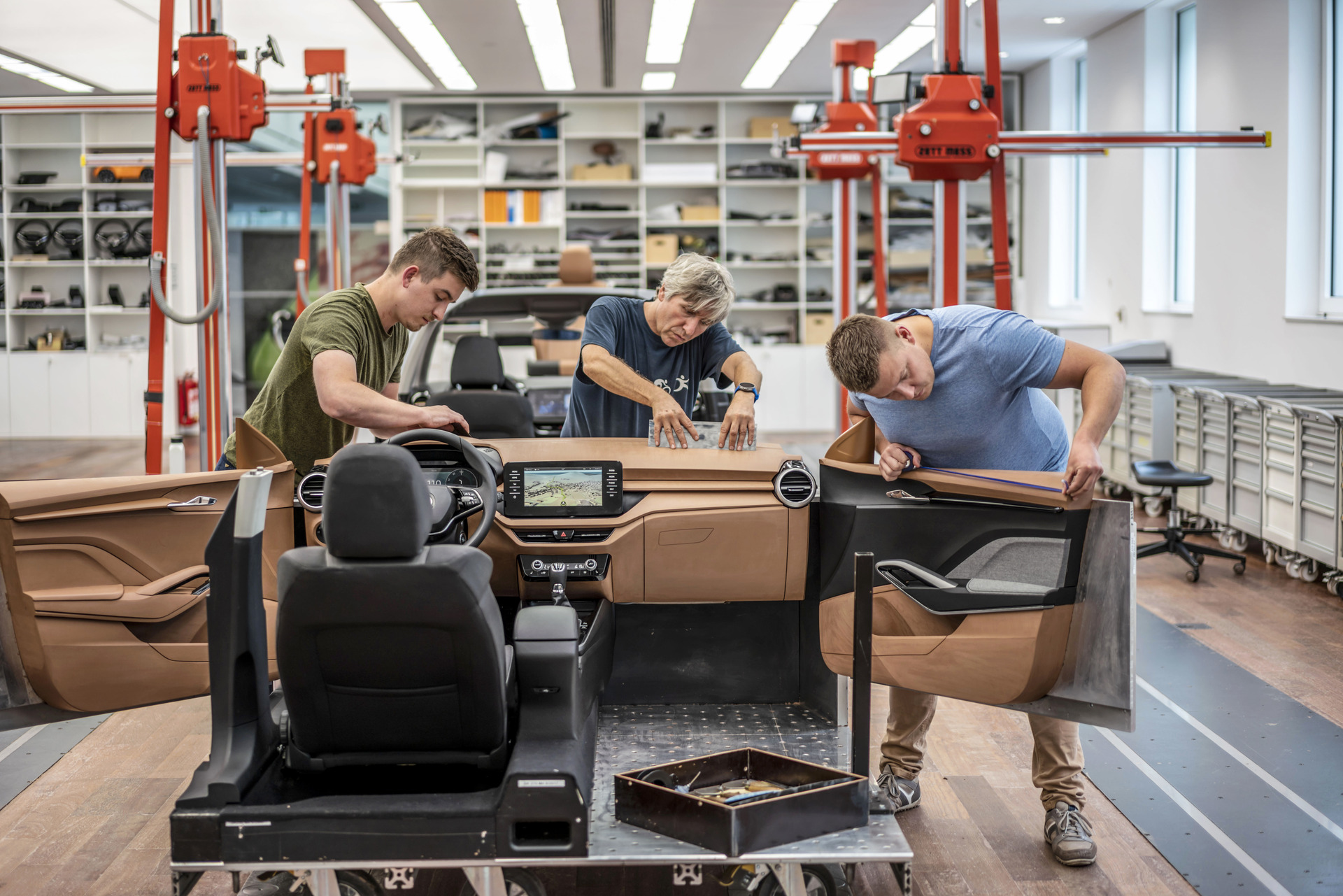
Für die Lackierung dieser Komponenten ist eine eigene Lackiererei zuständig. Auch das Karosseriemodell wird entweder lackiert oder mit einer speziellen Folie überzogen, sodass das Ergebnis aus einiger Entfernung wie ein echtes Auto aussieht. Wenn das Design perfekt ist, wird ein Hartmodell gefertigt: Dieses besteht nicht mehr aus Ton, sondern aus festen Materialien, die sich im Laufe der Zeit nicht verformen. Die Herstellung dieser Modelle wird in der Regel extern vergeben und stützt sich auf die Daten und Erfahrungen, die bei der Herstellung des Tonmodells gesammelt wurden. „Bei diesem Modell sieht fast alles vollkommen echt aus. Chromteile müssen verchromt sein, die Scheinwerfer funktionieren und das Modell ist sogar fahrbereit. Dieses Modell bildet ‚die Spitze der Pyramide‘. Es ist das Modell, das wir innerhalb des Konzerns präsentieren, über das wir uns mit anderen Marken austauschen oder das wir ausgewählten Partnern vorstellen“, sagt Vlastimil Pažout.
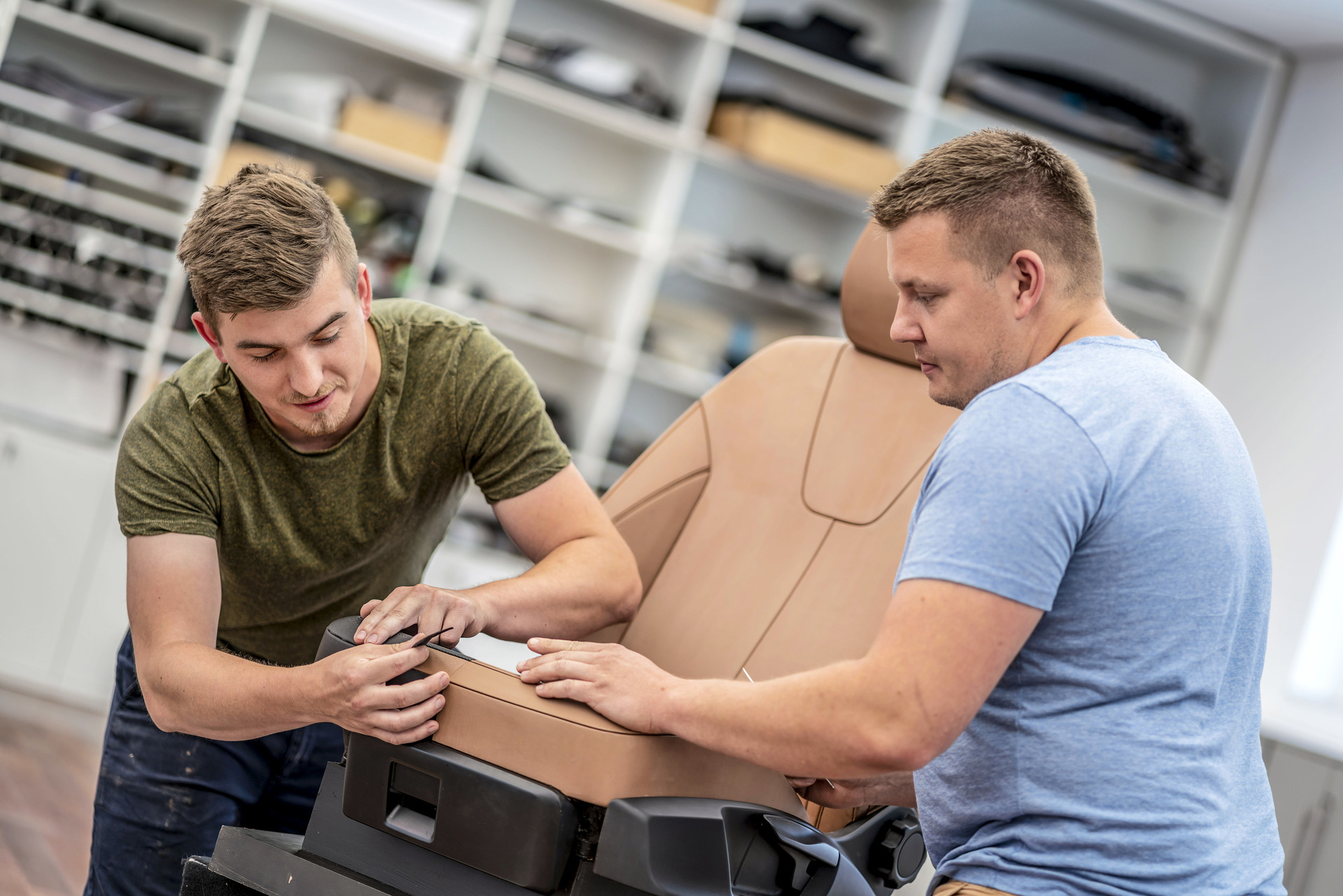
Die Tonmodelle werden für gewöhnlich in einem klimatisierten Lager aufbewahrt und kommen dann wieder zum Einsatz, wenn die Modernisierung eines Fahrzeugs ansteht. Danach ist ihr Lebenszyklus in den meisten Fällen abgeschlossen – sie werden nicht unbegrenzt gelagert. Die Arbeit der Abteilung Entwurfsmodellierung und Digitalisierung an der endgültigen Form der Modelle und damit auch am endgültigen Design eines Fahrzeugs nimmt etwa zwei Jahre in Anspruch. Mehrere Dutzend Personen arbeiten am Entwurf, der geheim bleibt und die Grundlage für die Herstellung der ersten Prototypen bildet.